Arc Welding Equipments
Some very important items used by a welder with an arc welding machine during
the welding operation, are called arc welding accessories.
- Electrode holder
- Earth Clamp
- Welding cables/ leads
Electrode holder
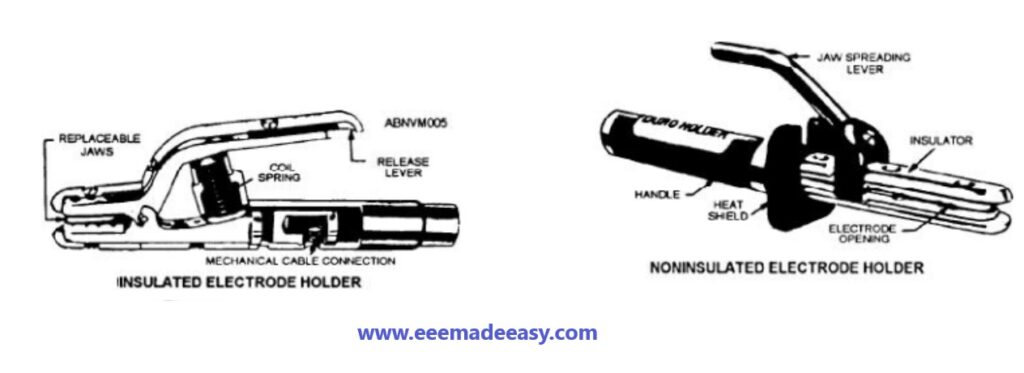
Electrode holder is a clamping device used to grip and manipulate the electrode during arc welding.
It is made of copper/ copper alloy for better electrical conductivity. Partially or fully insulated holders are made in various sizes i.e. 200-300-500 amps.
The electrode-holder is connected to welding machine by a welding cable.
Download & Install EEE Made Easy App
Earth Clamp
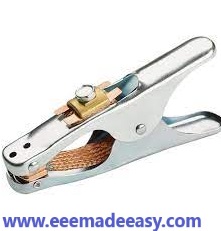
It is used to connect the earth cables firmly to the job or welding table. It is also made of copper/ copper alloys.
Screw or spring loaded earth clamps are made in various sizes i.e. 200-300-500 amps
Welding cables/ leads
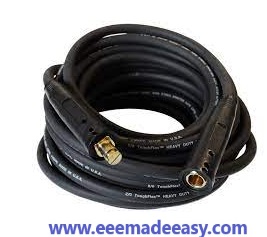
These are used to carry the welding current from the welding machine to the work and back.
The lead from the welding machine to the electrode-holder is called electrode cable and the lead from the work or job through the earth clamp to the welding machine is called earth (ground) cable.
Cables are made of super flexible rubber insulation, having fine copper wires and woven fabric reinforcing layers. Welding cables are made in various sizes (crosssections) i.e. 300, 400, 600 amps etc.
The same size welding cables must be used for the electrode and the job.
The cable connection must be made with suitable cable attachments (lugs).
Loose joints or bad contacts cause overheating of the cables.
MATERIAL PREPARATION METHOD
Welding material preparation Methods are,
- cutting
- Cleaning
Cutting
Cutting and preparing the base metal to the required dimensions from the original material available is necessary before welding them.
Different methods used to cut metals are:
- By chiseling the sheets
- By hack-sawing
- By shearing using hand lever shear
- By using guillotine shear
- By gas cutting
For thin sheets the first 4 methods are used. For thick materials method 2, 4 and 5
are used.
Tools and equipments used to cut metals
- Cold chisel
- Hacksaw with frame
- Hand lever shear
- Guillotine shear
- Oxy-acetylene cutting torch
The cut edges of the sheet or plate are to be filed to removed burrs and to make
the edges to be square (at 90° angle) with each other.
For ferrous metal plates, which are
more than 3mm thick, the edges can be prepared by grinding them on a bench/ pedestal
grinding machine.
Cleaning
The base metals before cutting them to size will have impurities like dirt, oil, paint, water and surface oxides, due to long storage.
These impurities will affect the welding and will create some defects in the welded joint. So in order to get a strong welded joint, it is necessary to clean the surfaces to be joined and remove the dirt, oil, paint, water, surface oxide etc. from the joining surfaces before welding.
Importance of cleaning
The basic requirement of any welding process is to clean the joining edges before
welding.
The joining edges or surfaces may have oil, paint, grease, rust, moisture, scale
or any other foreign matter.
If these contaminants are not removed the weld will become porous, brittle and weak.
The success of welding depends largely on the conditions of the surface to be joined before welding.
Methods of cleaning
- Chemical cleaning includes washing the joining surface with solvents of diluted hydrochloric acid to remove oil, grease, paint etc.
- Mechanical cleaning includes wire brushing, grinding, filing, sand blasting,scraping, machining or rubbing with emery paper.
- For cleaning ferrous metals a carbon steel wire brush is used.
- For cleaning stainless and non-ferrous metals, a stainless steel wire brush is used.
Read more on Electric Welding
- [Set 2]MCQ’s on Electrical Welding|Electrical Welding MCQ Questions and Answers|KSEB Sub Engineer
- [Set 1]MCQ’s on Electrical Welding|Electrical Welding MCQ Questions and Answers|KSEB Sub Engineer
- Electric Welding|Resistance welding Electric Arc Welding
- Resistance Welding|Types of Resistance Welding
- Electric arc welding|Types of Electric Arc welding
- Electric Arc length|Short,Medium, Long Arc
- Open Circuit voltage and Arc voltage|Polarity in arc welding
- Arc Welding Equipments|Arc Welding tools and Accessories
- Arc welding safety|shielded metal arc welding preparation & safety
- Methods of joining metals|Metal Joining Methods
- Types of welds|Weld types
- Applications of Welding|Welding Applications
Books on Welding
Join EEE Made Easy Telegram channel
- Industries Extension Officer Syllabus Kerala PSC|IEO 2024 Syllabus
- [PDF]Trade Instructor Gr.II Electroplating Syllabus Kerala PSC|92/2023 syllabus
- [PDF] Syllabus Assistant Engineer Electrical Harbour Engineering Kerala PSC
- Industries Extension Officer Kerala PSC Notification|IEO 2024
- Electricity Act 2003 Section 135
- Synchronous Motor Advantages, Disadvantages & Applications
- [Latest]Assistant Director industries and commerce Kerala PSC syllabus|630/2023 syllabus